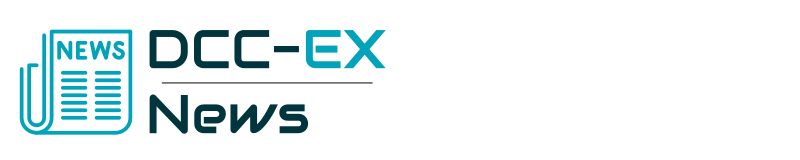
DCC++ VS DCC-EX?
Everything you loved is still there…
First, we want to stress that we didn’t break anything!
Whether you are using JMRI as a controller/front-end to send commands to your track, handle turnouts/points, read and write CVs, or using any other software or the serial monitor, the commands are still the same. We have expanded the API (Application Programming Interface) to add new commands and provide new responses, but they won’t affect your old control methods. One example of a new command is the one to handle turning power on and off to individual tracks.
EX-CommandStation is all new!
While we made minor changes to the original DCC++ “BaseStation-Classic”, all new development is going forward with the EX‑CommandStation. At first, we expanded features, added functionality, and fixed bugs by working from the existing code base.
The updated BaseStationClassic (DCC++) release of DCC++ will be familiar to any of you who played with the code. However, we want to stress that the newer releases, EX‑CommandStation, are a complete re-write from the ground up and is greatly improved.
What’s different?
We added many new functions such as:
Individual track power control
Programming track turned on automatically when programming and off when finished
User add-on functions (intercept commands to route to your own routines)
Much simpler Function (F0-28) command
EXRAIL Automation and/or accessory control
HAL - Hardware abstraction layer to make adding new types of hardware simple
Extended functions up to 68
Better turnout/point handling
Servo support
Built-in wiThrottle Server to directly support wiThrottle Protocol based throttles
Built-in support for the LCN node based accessory bus
Support for more motor drivers
Easy to create motor definition for motor drivers not in our current list
LCD and OLED display support
WiFi, Ethernet, and Bluetooth support
An easy to use Installer
Nano and Teensy support
ARM Cortex M0 and M4 support
New DCC-EX features added to JMRI like a current monitor display
Custom add-ons for Engine Driver including Routes and Automations on buttons
28 speed step support in addition to 128
Extensive logs and diagnostics in a serial monitor or the JMRI DCC++ log window
Created many new commands
Developed a new browser based throttle (EX-WebThrottle)
New “DriveAway” feature to be able to recognise a loco on a siding used as a programming track and drive off of onto the main track
… and much, much more.
How did we do it?
We assembled a team of software developers and electronics engineers from around the world, created a plan, and started work early in 2020. (See the team information and credits on the About page)
We started with the DCC Signal Generation code, what we call the “Waveform Generator”. We got together as a team and looked at how we could make it better. It soon became clear that rather than make piecemeal changes, the entire concept of how the signal could be generated, and how to use timers and interrupts, would need to be re-imagined. This not only sped things up considerably, but allowed us to allow you to connect some shields right on top of your Command Station board without jumpers!
Next we focused on packet generation. We looked at the complexities of reading and maintaining code that was using binary math, multiple “registers” to hold train data, and doing bit shifting everywhere to build bytes and stuff them into data packets. The new method gets rid of the old registers and simplifies the whole structure for building packets. Things like start and stop bits and preamble bits are static pieces of information. So being able to just insert them where they need to go saves time and processor bandwidth.
We created an internal API for how modules communicated with each other, so the code is more modular and each unit is dedicated to its specific task.
We completely re-wrote current sense and ACK detect routines to better protect your trains and make programming more accurate. There are complete diagnostics to allow you to see see exactly why a particular decoder is not reading or writing, and we provide settings you can add to your configuration to get it to work in most cases.
Why did we do this?
First and foremost, we just wanted to have fun. We saw an engineering problem and we wanted to tackle it. As is the case with most engineers, we thought we could do it better than anyone else. ;) Second, we saw an opportunity to provide something really amazing to the Model Railroad Community for low cost and that worked as well or better than anything on the market.
Details to Make Engineer’s Propellers Spin
We needed a platform that would allow us to grow into the future. The first thing we found was that in order to allow easy changes and to be able to adapt to technology we might want to use going forward, the code needed to be more modular. Each unit needed to be a “black box” that either did just one task and did it well, or take input and generate output without having to know anything about the module it was communicating with. Therefore, we created an internal API through which the modules could communicate. By simply unplugging one unit and plugging in another we could continue to work using different devices. An example of this is input and output. It doesn’t matter whether JMRI is sending commands to the EX‑CommandStation or if it is a wireless Cab Controller. It doesn’t matter if the output device is the serial monitor or an I2C display. It doesn’t matter if you want to use a serial port or a network device to route data. This makes it very easy to implement new features with new devices. We just have to create a small interface for whatever new device we want to implement. This has the side benefit of allowing the code to be more readable.
Next, the Waveform Generator needed 2 timers and interrupts, one for the Main track signal and one for the Programming track. The Uno only has 3 timers. So 2 of them were already tied up for sending the DCC signal. Since the programming track sits idle most of the time, and both signals were always being generated to the input of the motor board, processing power was being wasted that could be put to use for something else. In addition, because of the way the Arduino is designed, we were forced to use jumpers to connect pins on the Arduino to those on the motor board. Our new design eliminates the need for jumpers!
The packet generation routine was complex, hard to maintain, and limited us with regard to the hardware we could run on and new features we could implement (like the Railcom cut-out). We replaced the slow DigitalRead() and DigitalWrite() routines with a fast write library. The packet generation is now streamlined, fast (which allows us to be able to use only 1 timer to create signals for 2 tracks), and much easier to read.
We made a huge effort to streamline the code and optimise it for microcontrollers to use the limited memory we have available in the most efficient manner. The code is now object oriented and utilises classes for readability and reusability. We eliminated almost all use of strings.
The 3 most requested features were: 1. More reliable CV read and writes, 2. Better accessory control, 3. Automation. Some have requested a Railcom cut-out. We haven’t limited ourselves to just these features, but we put a lot of time into redesigning things to accommodate them.
The current detection routines are completely different. One key difference is all current readings are in milliAmps (mA) instead of meaningless pin readings. So if you want to set your overload protection to kick in at 3 Amps, you just enter 3000 for 3000mA instead of looking up a value from a table.
We continue to test all the motorboard and Arduino combinations at different voltages to refine our current readings. This is important because we want to have accurate and fast short-circuit detection, and because the reason CV reading was occasionally unreliable in the past was due to not always sensing a current pulse on the track. In addition to more accurately reading current, we had to completely change the way we look for an “ACK” (acknowledgement from the train that it received a command). So we now check immediately after we send a command instead of waiting for a dozen or more packets. This means we don’t miss an ACK while this is happening, and we jump out of sending unnecessary packets as soon as we get one. We also use our knowledge of CVs and the probability of what a CV may contain, so save time by skipping ahead if our first guess is correct. You will appreciate how much faster we can read CVs now!
There are now full diagnostics for trying to determine why a particular decoder may not be reading or writing correctly and new commands to adjust parameters to deal with decoders that are not in compliance with NMRA specifications. We use resolution down to the microsecond.
We not only are working on a RailCom cutout within the Command Station, but are developing a way of reading the RailCom data and reporting it.
Automation
EXRAIL (Extended Railroad Automation Interface for Layouts) brings new capability to the world of automation. You don’t have to be a programmer to write a script that tells a train to start moving forward at a set speed until some action (like reaching a sensor) occurs! We will be providing a document and tutorial on EXRAIL once Beta testing is complete. This will be an open-ended project, since who knows what things people will come up with that they want to automate! It will be easy to extend the commands to handle whatever your imagination can dream of.
The bottom line
So while maintaining proper deference to Gregg Berman’s original concept of an inexpensive Command Station based on the Arduino platform, we don’t want to do a disservice to DCC-EX or developers like Chris Harlow (UkBloke), Harald Barth, Neil McKechnie, Dave Cutting, and others, who brought a new vision to the project, and who used very little of the original code. This is NOT DCC++ v2.0, this is a completely new, yet API and feature compatible, Command Station. And just a tease: What Command Station would be complete without a wireless Cab Controller that speaks DCC++? Keep looking at our web page for new announcements…
Thanks
This is a team effort. There are a dedicated and organised group of about 15-20 core people involved in the project. In addition, there is all of you who contribute with your comments, feature ideas, evangelizing and testing. So we give you our heartfelt thanks. We will see you online!
Click here for The DCC-EX Team Credits
Fred Decker October 2020